In partnership with NAMIC, NUS Centre for Additive Manufacturing (AM.NUS) and Interplex Holdings Pte. Ltd. has recently concluded their project on additively manufacturing Nitinol stents for medical applications using Selective Laser Melting (SLM) technique. This project has received support under NAMIC’s Full Project Funding Scheme.
What are Nitinol Stents?
Additive manufacturing (or 3D printing) of Nitinol allows a tooling-free fabrication of complex device geometries with desired porosity, composition, density, near-net-shape, while requiring little post-processing. Nitinol is a metal alloy comprising of Nickel and Titanium with material properties ideal for implantable devices. It is highly sought after in the medical industry for its three key properties:
Shape Memory: A deformed alloy is able to return to its initial non-deformed state under temperature control
Super Elasticity: A super-elastic alloy deforms reversibly in response to applied stress
Good biocompatibility: Biocompatible materials are compatible with living tissue and do not produce a toxic or immunological response when exposed to the body or bodily fluids
These properties of Nitinol result in the suitability of its usage in self-expanding medical stents , which are small tube-like surgical devices typically used by surgeons to unblock or widen clogged arteries to restore regular blood flow in minimally-invasive vascular surgeries.
According to the World Health Organisation [1], 17.9 million people die from cardiovascular diseases every year, which makes up an estimated 31% of total deaths globally. With the colossal number of deaths from cardiovascular diseases and the increasing demand for minimally-invasive surgical procedures (growing at an expected CAGR rate of 9.85% from 2015 to 2026) [2], the global demand for Nitinol-based medical devices is forecasted to grow as well, at a CAGR rate of nearly 11% from 2017 to 2021 [3].
Traditional Methods of Manufacturing Nitinol Stents
Laser Cutting
A popular method for manufacturing Nitinol stents, laser cutting involves cutting a cylindrical Nitinol tube into a stent’s pattern of struts using a laser beam while the tube rotates around its longitudinal axis. The process of forming complex stent structures is limited by the “parent” tube, in which the shape and size of a laser cut stent is dependent on.
Braiding
This process involves Nitinol wires being braided into the designed patterns, usually utilizing tooling and fixtures. However, this process is labour-intensive and customization of the stents is limited as different fixtures need to be fabricated for different stent designs.
3D Printing Nitinol Stents via Selective Laser Melting (SLM)
3D printing technology has the capability to produce metallic parts with delicate geometric features, while at the same time enabling customization at lower labour cost as digitized CAD files are used for printing, in place of tooling and fixtures.
The NUS-Interplex project utilized SLM to develop superior Nitinol stents that meet medical device standards (reference ASTM F2063-05). SLM is a laser-activated powder-bed-fusion process whereby metallic powders are melted and fused via a high power-density laser. The relationship between the 3D printing process (including powder preparation and post-processing via heat treatment) and Nitinol properties/microstructures were investigated in this project.
Key Project Outcomes
The NUS team successfully developed and demonstrated 3D-printed super elastic (shape memory effect) Nitinol stents with novel designs, becoming one of the earliest inventions in the medical industry on a global scale.
Following their development, a provisional patent has been filed on the 3D printed designs, optimal SLM process settings, as well as the methods on how to produce 3D printable Nitinol stents with the required mechanical properties and phase transformations. Interplex, a Singapore headquartered conglomerate, has indicated their interest to license and lead on the commercialization of AM Nitinol stents.
Three key milestones were achieved:
- Establishing the process-structure-property relation of Nitinol stent fabricated via SLM with optimized printing parameters, in accordance to ASTM 2063-05 standards and thus allowing for patient-specific customization of functional and mechanical properties of stents.
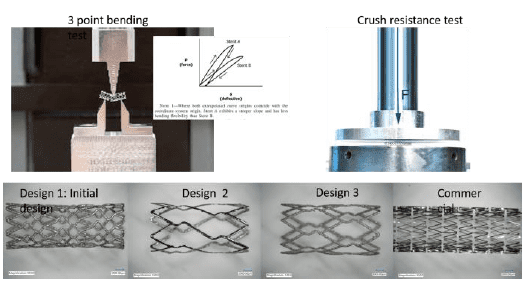
- Developing design for additive manufacturing (DfAM) guidelines for 3D printable Nitinol stents. 3D printing was utilized to produce prototypes of functional Nitinol stents with novel 3D printable designs.
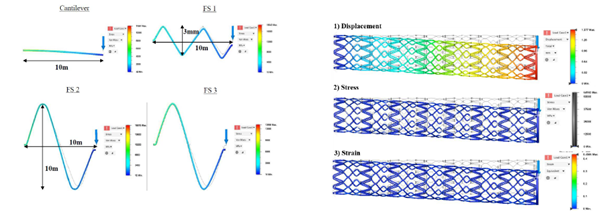
- Stent functionality was determined by conducting mechanical and biological tests.
Over the course of the project, one of the key challenges the research team faced was to determine the most optimal set of printing processing parameters using SLM technology, based on a complex causal process-structure-property relationship. Despite this, through a number of design-of-experiments, the team was able to identify the critical processing window to control phase transformation and the starting temperature for martensitic/austenitic phase to achieve the desired super-elasticity in the material.
With the success in demonstrating 3D printed Nitinol stents, the NUS team is currently working with Interplex to freeze the stent design and processes to deliver a product for clinical trials and regulatory (i.e. FDA, HSA) approval. Concurrently, market studies together with Medical device OEM companies will be conducted to develop a go-to-market strategy for 3D printed stents.
References
[1] ‘Cardiovascular Diseases’ by World Health Organisation
[2] ‘Minimally Invasive Surgical Instruments Market Size, Share & Trends Analysis Report By Device (Handheld Instruments, Inflation Devices), By Application (Cardiac, Gastrointestinal), By End Use, And Segment Forecasts, 2019 – 2026’ by Grand View Research, October 2019
[3] ‘Nitinol-based Medical Devices Market – Drivers and Forecasts by Technavio’ by Business Wire, September 2017
NUS Centre for Additive Manufacturing Address: 3 Research Link, I4.0 Building, #05-01 Singapore 117602Phone: +65 6516 6666Email: [email protected]LinkedIn: ILO NUSWebsite: https://am.nus.edu.sg/ | Interplex Holdings Pte. Ltd.Address: 298 Tiong Bahru Road #17-01 Central Plaza #17-01, 168730Phone: +65 6264 0033LinkedIn: InterplexWebsite: https://interplex.com/ |