The objective is to develop gas atomisation process to produce nickel aluminium bronze powder, including heat treatment to meet the material specification from the maritime industry. The project demonstrated the gas atomisation as a scalable processto produce AM powder, and is a feasible feedstock for emerging AM process like cold spraying for part fabrication. The powder is also applicable for laser powder bed fusion process and laser directed energy deposition processes.
Singapore Polytechnic
Innovation Centre for Additive Manufacturing (ICAM) is an end-to-end additive manufacturing hub located at Singapore Polytechnic. ICAM’s facilities, advanced capabilities, and a team of expert personnel specializing in materials science, mechanical engineering, and computational design, enables them to offer a comprehensive suite of additive manufacturing solutions, from materials development to post-processing. Upon the completion of research & development, ICAM works closely with industry partners as well as material suppliers, service bureaus, accredited testing labs and certifying bodies to drive AM adoption and commercialisation. For specific interest in AM metal powder customisation, industry can leverage ICAM’s unique expertise and its in-house gas atomisation plant.
As a joint effort between National Additive Manufacturing Innovation Cluster (NAMIC), Enterprise Singapore (ESG) and Singapore Polytechnic, ICAM accelerates AM innovations for high-value commercial outcomes and bridge the gap in talent development for a skilled AM workforce.
With a comprehensive state of the art equipment and expertise, we strive to tackle industry challenges and needs through collaboration in the following industries.
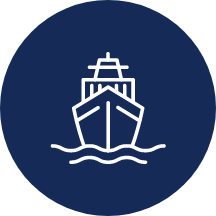
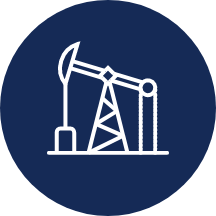
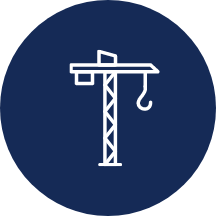
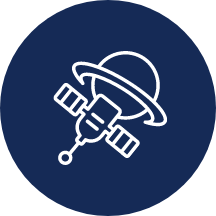
Providing a wide range of facilities and equipment to accelerate the adoption of Additive Manufacturing across multiple industries.
AM Technology: laser PBF-Metal
Build Size: ø100 × 100 mm
Choice of Materials: Stainless Steel
AM Technology: laser PBF-Metal
Build Size: 250 × 250 × 300 mm
Choice of Materials: Stainless Steel
Technology: laser DED + 5-axis CNC mill
Build Size: ø500 × 365 mm
Workpiece size: ø650 × 500 mm (max)
Choice of Materials: Stainless Steel
AM Technology: Material Jetting
Build Size: 490 × 390 × 200 mm
Choice of Material: Proprietary Resin such as Tango Family, Vero Family, Rigur and Durus, Support 705
AM Technology: Material Extrusion
Build Size: 355 × 254 × 252 mm
Choice of Materials: Proprietary Filament such as ABS, ASA, PC-ABS, Nylon-12, Ultem etc.
AM Technology: Material Extrusion
Build Size: 330 × 240 × 240 mm
Choice of Materials: ABS, PLA etc.
Technology: Metal Powder Size and Shape Characterization Equipment
Powder measuring range: 1 µm to 3 mm
Technology: Gas Atomisation for Additive Manufacturing Metal Powder
Customise Metal Powder for Laser PBF, Laser DED, Cold Spray, etc
Customise Metal Powder for various alloys, such as iron-based, nickel-based, aluminium-based, cobalt-based, copper-based, High Entropy Alloys, Metallic Glass
Technology: 5-axis CNC mill
Workpiece Size: ø630 × 500 mm (max)
To learn more about the equipment and facilities at SP ICAM, please visit here.
Explore the breakthrough of additive manufacturing through constant research & development projects.
The objective is to adopt AM to produce turbocharger nozzle ring so that the lifespan and performance of the part are optimised for ship vessel. The project is a consortium led by Lloyds Register, together with LRQA, 3D Metalforge, Singapore Polytechnic, Neptune Pacific Lines, Kompressorenbau Bannewitz GmbH and Professional Testing Services. Singapore Polytechnic has also demonstrated the production of high-performance powder as AM feedstock via in-house gas atomisation facility.