Most of the current foetal heart rate monitoring devices are fabricated with hard materials that often discomfort the users. Furthermore, due to its rigid and bulky nature, it cannot be used for a long period of monitoring, nor can it conform to users of various sizes. Objectives are to examine soft biocompatible materials for the substrate, electrodes, and circuit, to develop a 3D printing wearable circuit which can effectively connect the electronic components, and to fabricate a functional prototype of the proposed wearable device.
National University of Singapore
The NUS Centre for Additive Manufacturing (AM.NUS) leverages the National University of Singapore (NUS)’s world-class faculties, expertise and advanced capabilities in 3D printing technology, to bring innovative products to the market.
AM.NUS is the only multi-disciplinary Additive Manufacturing (AM) centre in an Institute of Higher Learning in Singapore which comprises the following Faculties (Medicine, Science, Dentistry and Design & Engineering). The Centre is supported both internally by NUS and externally by National Additive Manufacturing Cluster (NAMIC) and Singapore Economic Development Board.
Bringing together a multi-disciplinary expertise through the collaboration between various schools and faculties in the following industries.
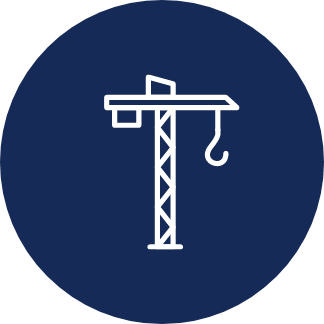
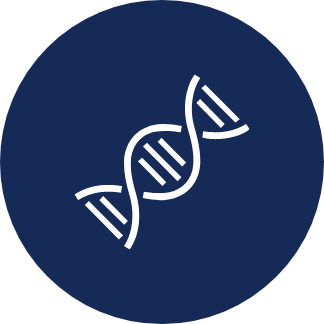
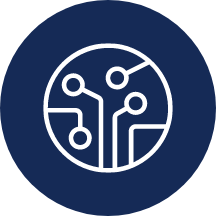
Providing a wide range of facilities and equipment to accelerate the adoption of Additive Manufacturing across multiple industries.
AM Technology : DMLS
Choice of Materials : Stainless Steel, Maraging Steel
Build Size: 250x250x325 mm
Laser Focus Diameter: 100 µm
Minimum Layer Thickness: 20 µm
AM Technology : SLM
Choice of Materials : Aluminium, Steel, Titanium, Nickel & Cobalt Chrome Alloys
Build Size: D140 x H190 mm
Resolution (Spot Size): 80 µm
Minimum Layer Thickness: 10 µm
AM Technology : Extrusion
Choice of Materials : Biomaterials and Cells
Build Size: 100x346x40 mm
Resolution: 2 µm
Minimum Layer Thickness: 10 µm
AM Technology : SLM
Choice of Materials : Titanium Alloys
Build Size: 250x250x350 mm
Laser (Spot Size): 75 µm
Minimum Layer Thickness: 20 µm
AM Technology : Polyjet
Choice of Materials : Vero™, VeroVivid™, Tango™, Agilus30™, VeroClear™, Digital ABS Plus™, Rubber-like materials, Translucent color tints, SUP705 (waterjet removable)
Build Size: 490x390x200 mm
Resolution: 14-27 µm depends on speed and quality
Minimum Layer Thickness: 14 µm
AM Technology : Lithography-based
Choice of Materials : Photosensitive resin with homogeneous dispersed alumina or zirconia
Build Size: 76x43x150 mm
Lateral Resolution: 423 dpi
Minimum Layer Thickness: 25 µm
AM Technology : Ink Jet, Aerosol Jet, FDM, CNC, Light Beam
Choice of Materials : Nanoparticle & micron scale particle inks, adhesive dielectrics and quantum dots
Ink Jet
Printing Speed: 20 mm/s
Ink Viscosity: up to 28,000 mPas
Resolution: 100-300 µm
Aerosol Jet
Printing speed: 5 mm/s
Ink Viscosity: up to 20 mPas
Resolution: 40-50 µm
AM Technology : SLS
Choice of Materials : Polyamides PA2200, PA2241FR, Aluminide, CarbonMide
Build Size: 340x340x600 mm
Laser Spot Size: 500 µm
Minimum Layer Thickness: 60 µm
AM Technology : Extrusion
Choice of Materials : Self-developed materials, Open source materials
Build Size: 130x90x70 mm
Resolution: 10 µm
Minimum Layer Thickness: 2 µm
To learn more about the equipment and facilities at AM.NUS, please visit here.
Explore the breakthrough of additive manufacturing through constant research & development projects.
An adventure of 3D printing of Nitinol stent started in 2018 under a collaborative project between AM.NUS and Interplex Precision Technology (Singapore) Pte Ltd. This project aims to design and develop superior Nitinol stents using SLM technology that could meet medical requirements. The relationship between the 3D printing process (including powder preparation and post-process heat treatment) and Nitinol properties/microstructures are also being investigated.