The ability to design and fabricate lightweight structure is one of the most important aspect for building a drone system. Often, connecting wires are used on the drone system for powering and signal transmission at the expense of the drone’s weight. In this project, we explore the design and fabrication of a safety cage for drone using design optimization and 3D printing. A hybrid 3D printing process is proposed for the fabrication of lightweight multifunctional structure with printed circuit for a drone safety cage. The safety cage is designed in such a way that maximizes the production efficiency of 3D printing processes. In addition, aerosol jet printing is used to fabricate conformal circuit onto the 3D printed safety cage structure to replace the conventional connecting wires for weight saving purpose. Lastly, an electrical characterization is conducted to investigate the functionality of the printed conductive traces on the safety cage.
Nanyang Technological University
NAMIC Hub @ NTU also known as Singapore Centre for 3D Printing (SC3DP) drives research development and industry adoption of additive manufacturing technology through collaborative projects with leading industry partners, and with schools and research centres within and beyond NTU.
SC3DP has identified the following key industry areas that would benefit from the introduction of new capabilities and know how, and works closely with the respective industry partners on their specific needs.
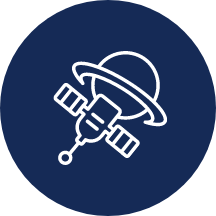
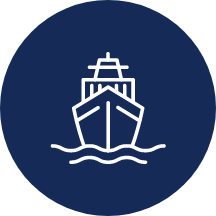
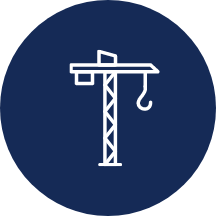
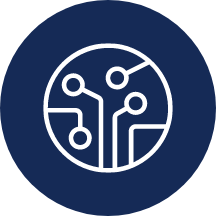
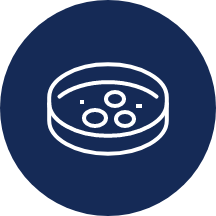
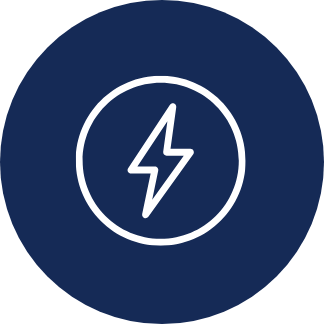
Providing a comprehensive suite of integrated end-to-end additive manufacturing facilities for the research innovation of industry-ready solutions.
DED Technology – DMG Mori Lasertec 65 with 5-axis CNC milling
Build size: Ø650 x 500mm
Materials: Stainless Steels, Tool Steels, Cobalt Chrome, Bronze, Nickel Superalloys, in-house developed materials
Others DED system: BeAM MAGICS 800, TRUMPF TruLaser Cell 3000
Laser Powder Bed Fusion Technology – SLM500HL (Dual lasers)
Build size: 500 x 280 x 325mm
Materials: Stainless Steels, Tool Steels, Cobalt Chrome, Nickel Superalloys, Copper and Copper Alloys, Aluminium Alloys, Titanium Alloys, in-house developed materials
Others powder bed fusion system: SLM250HL, EOS M290, EOS M100
Portable Laser metal deposition system – in-house developed
Build size: 1m x 1m x 1m
Materials: Stellite 6, Inconel 625, 4340 steel, Mn steel
Polymer printing SLS Technology – EOS P396
Build size: 340 x 340 x 600mm
Materials: Polystyrene, Polypropylene, Nylon-12, Glass and carbon composites, in-house developed materials
Others polymer printing system: Fortus 450MC, Connex 3, Formlabs Form 3 / 3L, ASIGA MAX (DLP), Sharebot (Snow white 2), Ultimaker 3, UP BOX, Cubicon style
Polymer Pellet Printing – Arburg Freeformer 300-3X
Build size: 234 × 134 × 230mm
Materials: TPE, PC, in-house developed
Multi-printhead Bioprinter – Cellink BIO X6
Build size: 128×90×90mm
Materials: Nanocellulose hydrogel, in-house developed materials
Others bio-printing system: RegenHU BioFactory, Bioplotter – Nordson EFD PRO4L
Concrete printing – Large scale Gantry Printer (in-house developed)
Build size: 6x5x3m
Materials: Plain concrete•Fiber reinforced cementitious composites•High volume fly ash concrete•Geopolymer•Shotcrete (Spray-based 3D Concrete Printing)•Magnesium potassium phosphate cement•Fluid catalytic cracking ash-blended cementitious composites•Marine Clay•Recycled Glass•Incinerator bottom ash (NEWSand)
Other concrete system: Small and medium scale Gantry Printer (0.6×0.5x1m & 1.2×1.2x1m), Denso Mobile Robot Printer (Spherical WorkspaceReach: 0.9m (Radius)), 6 Axis KUKA Robot Printer (Spherical WorkspaceReach: 3.9m (Radius))
PCB multi-layer printing – Nanodimension Dragonfly Pro 2020
Build size: 200 x 200 x 3mm
Materials: Dielectric ink, AgCiteTM conductive inks
Electronics printing – Optomec Aerosol Jet 5X
Build size: 200 x 300 x 200mm
Materials: Carbon Nanotubes, Graphene, Gold, Silver
To learn more about the equipment and facilities at SC3DP, please visit here.
Explore the breakthrough of additive manufacturing through constant research & development projects.
The inclusion of waste glass in landfill poses a global environmental due to the non-biodegradable nature of the glass material. Recycling the waste glass provides an innovative solution by recovering a major portion of the glass waste previously destined for landfill and converting it to clean, sized glass sand/powder. 3D concrete printing (3DCP) has been gaining attention in the building and construction industry in the past few years. This technology can increase construction productivity, save material and energy usage, and enable design toward structural optimization. The Building and Construction Group of SC3DP has developed a commercially viable 3D concrete printing media with recycled glass sand/powder as one of the main composites. This novel solution would help to improve the sustainability of the construction industry further.