This project is a development of software product and solution for automatic design and optimization of conformal cooling channels, which incorporates dynamic thermal analysis and assessment in a single system. The software could automatically Design and Optimize Conformal Cooling channels. As this software comes with a real-time dynamic thermal analysis, hot spots can be easily identified and corrected. It enhances the manufacturing productivity by improving part quality, reducing design lead time and tooling verification time. The solution also minimizes the dependence on human knowledge capital and solve the manpower intensive process in developing rapid tooling with conformal cooling.
Nanyang Polytechnic
The Additive Manufacturing Innovation Centre (AMIC) is a Centre of Excellence for Additive Manufacturing Technology & Design Innovations set-up jointly by EDB and NYP and located at Nanyang Polytechnic. The strategic intents of AMIC is to support the national AM initiatives to drive greater industry AM adoption and develop core capabilities in Design for AM optimization & process innovation, besides supporting the needs of NYP’s PET and CET programmes.
It also provides co-creation, collaboration and project incubation services for industry and conducts regular sharing sessions, clinics, etc.
Bringing together a team of experienced and competent professional Senior Lecturers, Development Engineers and Development Technologists in various technological areas to tackle industry challenges and needs in the following industries.
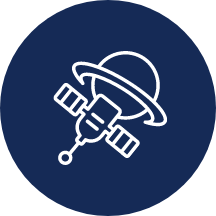
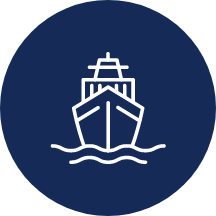
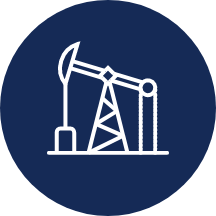
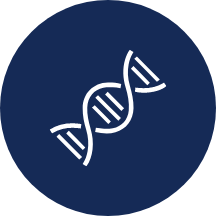
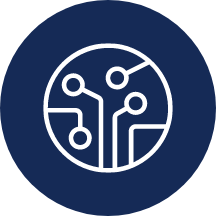
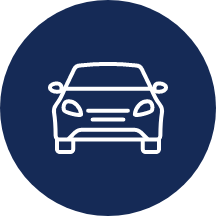
Providing a wide range of facilities and equipment to accelerate the adoption of Additive Manufacturing across multiple industries.
Process: Scanning of laser beam over the cross section of the model in the metal powder and building up layer by layer.
Material used: Stainless Steel, Maraging Steel (MS1), Aluminium (AlSi10Mg), Titanium (Ti64), Inconel 718
Maximum Build Size: 250mm x 250mm x 325mm
Laser Focus Diameter: 100 µm
Minimum Layer Thickness: 20 µm
Application: Rapid Tooling Insert with Conformal Cooling, Metal components, Hybrid prototypes, Other applications
Process: Scanning of laser beam over the cross section of the model in the metal powder and building up layer by layer.
Material used: Stainless Steel, Maraging Steel (MS1), Aluminium (AlSi10Mg), Titanium (Ti64), Inconel 718
Maximum Build Size: 250mm x 250mm x 325mm
Laser Focus Diameter: 100 µm
Minimum Layer Thickness: 20 µm
Application: Rapid Tooling Insert with Conformal Cooling, Metal components, Hybrid prototypes, Other applications
Process: Scanning of laser beam over the cross section of the model in the metal powder and building up layer by layer.
Material used: Stainless Steel, Maraging Steel (MS1), Aluminium (AlSi10Mg), Titanium (Ti64)
Maximum Build Size: 250mm x 250mm x 280mm
Minimum Layer Thickness: 20 µm
Laser Focus Diameter: 90 µm
Application: Rapid Tooling Insert with Conformal Cooling, Metal components, Hybrid prototypes, Other applications
Process: Powder-based technology utilising IR energy to fuse powder with light-absorbing ink and detailing agent.
Material Used: Polyamide (PA 12)
Maximum Build Size: 380mm x 284mm x 380 mm
Min Layer thickness: 0.08 mm
Application: Conceptual model, Fit, form and functional applications, Functional prototypes, Other applications
Process: Scanning of UV laser beam over the cross section of the model in liquid resin and building up layer by layer.
Material Used: Accura 60(PC Similar)
Maximum Build size : 650mm x 750mm x 550mm
Min Layer Thickness: 30 µm
Application: Concept modeling, Form fit, assembly tests, Master pattern for vacuum casting, Models for stress optical checking, Other applications
Process: Inkjet print heads are used to deposit materials on demand onto a build platform. The material solidifies which allows to build layers on top of each other.
Material Used: Clear, rubberlike photopolymers, and tough high-performance thermoplastics. Able to combine many colors and material properties into one model.
Maximum Build size: 490mm x 390mm x 200mm
Min Layer Thickness: 16 µm
Application : Concept modeling, Form fit, assembly tests, Functional Prototypes, Transparent and rubber like model, Other applications
Process: The extrusion head heats the filament and ‘draw’ section of the part on the build platform. Model is built upwards in layer.
Material Used: ABS, PC, PC-ABS, Ultem
Maximum Build Size: 900mm x 600mm x 900mm
Minimum Layer Thickness: 125 µm
Application: Conceptual model, Fit, form and functional applications, Investment casting, Other applications
“Process: The extrusion head heats the filament and ‘draw’ section of the part on the build platform. Model is built upwards in layer.
Material Used: ABS, PC, PC-ABS, Ultem
Maximum Build Size: 400mm x 350mm x 400mm
Minimum Layer Thickness: 127 µm
Application: Conceptual model, Fit, form and functional applications, Functional prototypes, Other applications”
Process: The extrusion head heats the filament and ‘draw’ section of the part on the build platform. Model is built upwards in layer.
Material Used: ABS
Maximum Build Size: 254mm X 254mm X 254mm
Min Layer Thickness: 125µm
Application: Conceptual model, Fit, form and functional applications, Functional prototypes, Other applications
To learn more about the equipment and facilities at AMIC, please visit here.
Explore the breakthrough of additive manufacturing through constant research & development projects.